Plastic plugs stand out for their versatility and effectiveness among the numerous options available for sealing, protecting, and insulating components in various industries. Essential in applications ranging from simple home fixes to complex industrial systems, these small but mighty tools play a crucial role. Understanding their utility can significantly benefit project managers, DIY enthusiasts, and professionals. Keep reading to discover how selecting the right plastic plug can make a difference in your projects.
Benefits of Choosing Plastic Plugs for Sealing Applications
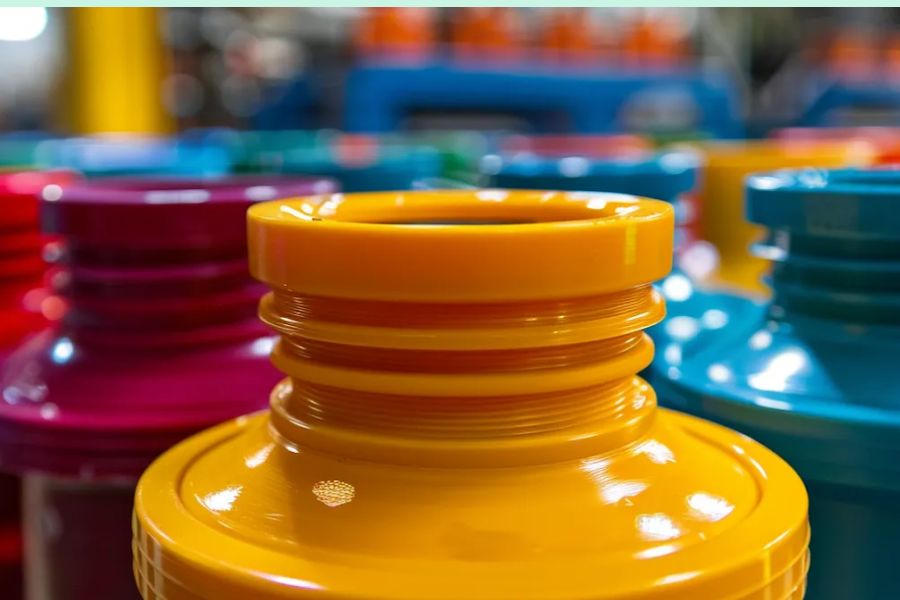
Plastic plugs have a significant edge over their counterparts in terms of sealing effectiveness. They are designed to create a tight, secure fit that prevents leakage of materials, whether it be gases, fluids, or solids. This intrinsic capability to form an airtight seal aids in maintaining the integrity of systems, thereby preventing contamination and ensuring safety and hygiene, especially in fields like food and beverage or pharmaceuticals.
Another hallmark of plastic plugs is cost efficiency. They are typically more economical than metal plugs, not just in terms of initial purchase cost but also when factoring in their lifespan and maintenance. Plastic is less prone to degradation from oxidation or chemical exposure, which reduces the need for replacements and allows for extended use without compromising performance.
Ease of installation is a clear advantage. Featuring elements like ergonomic designs or threads, these plugs can be placed with minimal effort and without special tools. This user-friendly attribute saves time and labor, streamlining processes in production lines or during equipment maintenance. It’s an especially valuable trait for sectors where rapid assembly and disassembly are common occurrences.
In addition to function, plastic plugs can also benefit aesthetics. Available in various colors and finishes, they can blend seamlessly with equipment and machinery or stand out as necessary for visual inspection. The use of vibrant hues can be particularly effective in safety-critical applications where swift recognition of seal integrity is essential.
How Plastic Plugs Enhance Electrical Insulation

One of the standout roles of plastic plugs is electrical insulation. The non-conductive nature of many plastics makes these plugs perfect for protecting against electrical hazards. By isolating wires and terminals, they guard against short circuits and potential electrical fires, contributing significantly to the safe operation of electrical apparatus.
Plastic plugs also help maintain an assembly’s dielectric strength, resisting the flow of electrical currents in sensitive or high-voltage environments. In applications such as transformers, switchgear, or circuit breakers, the precision fit of these plugs can be critical in preventing arcing and preserving the integrity of the insulation system.
Beyond their insulating properties, plastic plugs safeguard electrical components from external factors such as dust, which could otherwise lead to malfunctions or failures. This protective function is invaluable in ensuring the reliability of electronic devices, from consumer gadgets to industrial controls. Such reliability is key to maintaining productivity and avoiding costly downtime.
For repair work or retrofitting, plastic plugs offer an optimal solution for quick fixes or adjustments. Their lightweight and customizable nature benefit technicians who might need to drill into control panels or machinery, effectively sealing and insulating newly created openings. These practical aspects make plastic plugs a staple in electrical work.
Custom Solutions: Tailoring Plastic Plugs for Unique Use Cases
Not all applications can be addressed with off-the-shelf plug designs. Custom solutions are often necessary to meet the unique demands of specific projects or industries. Working with manufacturers, clients can tailor plastic plugs to fit unusual dimensions, withstand unique chemical exposures, or display superior durability under strenuous conditions. It’s this customizability that sets plastic plugs apart in the marketplace.
Today, Manufacturers employ state-of-the-art techniques, such as 3D printing, to create prototypes and final products that match the customer’s specifications. This process ensures a precise fit and accelerates the time-to-market for new applications that require unique plastic plug solutions. Moreover, integrating client feedback quickly during the prototyping phase results in a highly optimized end product.
Sector-specific requirements can also drive the customization of plastic plugs. For instance, plugs that can withstand sterilization processes without degradation might be needed in the medical field. In construction, plugs with enhanced load-bearing capabilities might be demanded.
In an industry where innovation is key, the evolution of plastic plug design is continuous. Custom solutions mean they can evolve with the end-users technological advancements and dynamic needs. For those looking for a custom solution, communication with expert manufacturers can lead to the development of plastic plugs that meet and exceed the expectations of any given application.
Altogether, plastic plugs offer a versatile, cost-effective solution for sealing, insulating, and protecting components across various industries. Their customizability ensures they meet specific needs, making them indispensable in everyday and specialized applications.
For more updates and news visit: Nhentainef!